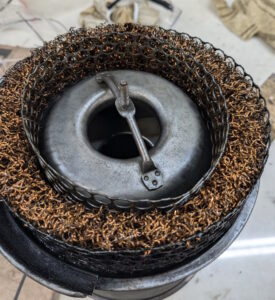
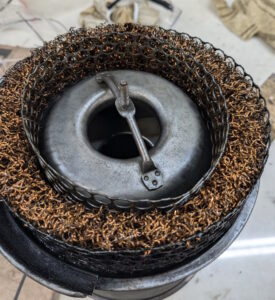
It is bound to get cold soon so I decided to jump on the nice weather while it lasts. I wanted to check out the oil pressure regulator while changing the oil but I seem to have misplaced the rebuild kit I bought a year or more ago. That really annoys me because I keep an up-to-date inventory of parts including where they are located but I must have missed the regulator kit. It is a tiny box and I probably put it somewhere clever and/or stupid. But for now I can just do the regular stuff.
Continue reading20 years or so ago I lucked into a guy who was street rodding a 41 Studebaker. I bought all the parts he did not want including a spare engine, overdrive transmission, and a differential. I always meant to tear into the diff to see if the brake drums were any good but never did. But when I was looking at the parts book I noticed that it showed a cover to keep road debris out of the parking brake slot. That was missing from my car so I decided to see if the covers were on the backup diff. I had to dig the axle out of the shed and haul it around to the garage, but I will spare you that part of the saga.
Continue readingI figured out more than a year ago that my flasher was the reason the indicator light in my turn signal switch is not working. I have tried a couple of flashers. I even took one apart to see if I could modify it. Nothing worked. So I decided to throw technology at the problem.
Continue readingLast night I got the third brake light installed but did not install the rear seat. Part of the reason is that there has been a loud squeak coming from back there and I want to take a stab at fixing it.
Continue readingOtherwise known as a third brake light. Since my feeble attempt at LED taillights almost 20 years ago (!!!) I have been trying to figure out what to do about the pathetic dim taillights on this car. I finally found a solution I like.
Now that the weather is warming up I decided to try and fix some of the damage done by my now-ex rebuilder. JB Weld to the rescue?!? There were two stripped holes on the carb. The plan was to find a nice long screw that fits each hole, oil them so the epoxy will not stick, clean the holes, then goop the screws in. Once the epoxy hardens the screws will hopefully come out and leave better threaded holes than I have now.
Continue readingBack in December I put the old brake shoes back on the car. I kinda knew this was a bad idea, and it turns out it was. The brakes did not work very well and squealed a lot. So, I am going to put the new shoes back on and get them right this time.
Continue reading12/17/2023 to 2/11/2024
When I was working on the brakes I found that the car would not idle. Stalled every time. It has been nearly 20 years (!!!) since I rebuilt the carb back in 2005 so I took it out to examine. This is going to be a long post, so buckle up.
Continue readingI left off the last post with the passenger side front brake locking up when the brakes were applied. Time has been short but over the last week or so I have been pecking away at it.
Continue reading